Sikorsky Product History
Sikorsky S-92
Background
The S-92 Helibus was designed and developed during the 1990 decade to serve as both a commercial passenger carrier and as a military troop/cargo carrier. Its initial design was intended to take advantage of the both the proven technologies of the Black Hawk models as well as the four million flight hours accumulated on the H-60 series at that point in their history. The H-60 dynamic system in particular had reached a proven high level of durability as a result of this extensive operating service experience. However, the initial design of the S-92 using the then existing H-60 propulsion and dynamic systems mated to an enlarged fuselage proved to be too limited in useful load capability. This limitation was created by a combination of the higher weight of a new airframe designed to carry 19 passengers and to the structural limitation of a 22,000 pound gross weight imposed by the existing H-60 dynamic system.
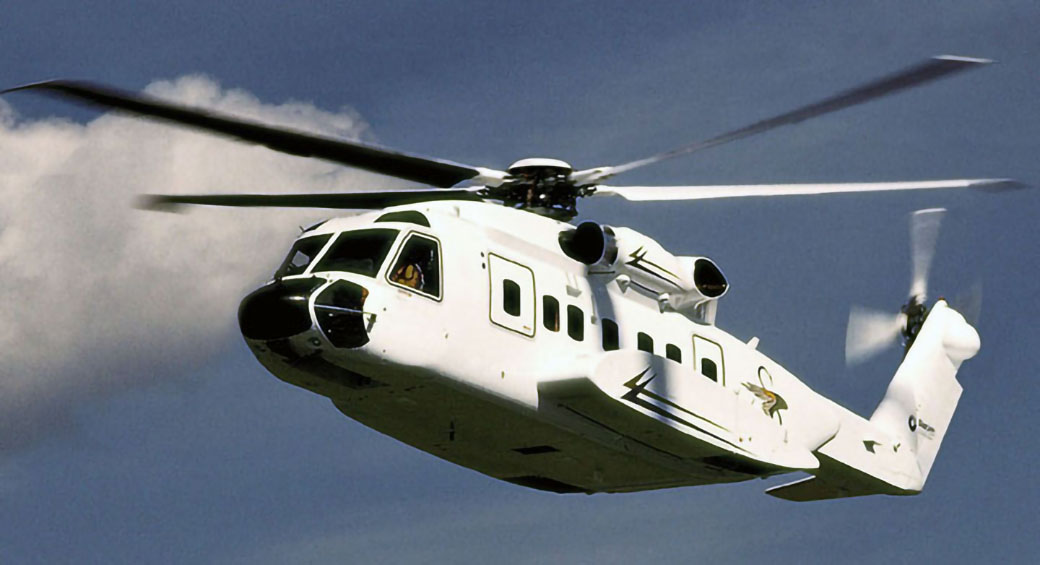
Because these limitations imposed too great a penalty on speed and range performance, the decision was made to redesign and upgrade the basic H-60 dynamic system where needed to achieve a mission gross weight closer to 25,000 pounds while at the same time designing the dynamic components to meet newly issued FAA requirements regarding damage tolerance for commercial helicopters. That effort was so successful that Sikorsky was awarded the 2002 Collier Trophy by the National Aeronautics Association acknowledging its achievements in safety, operating cost and traveling comfort. The S-92 design benefited from many new technologies that together represented a new helicopter generation. Chief among these were the advanced rotor blade that employed improved airfoil design and blade tip configuration as well as a fully composite material spar and a fully damage tolerant main rotor head design. In addition, Sikorsky’s new Active Vibration Control System provided much reduced vibration levels throughout the operation aircraft and rotor speed ranges. Significant cockpit display system improvements helped improve aircraft safety and reduced pilot workload. The reader should note that the S-92 and its derivative models were still in production at the time that this model history was prepared. As a result, changes to the design, equipment, features, weights and performance described herein are likely to take place as this model becomes further developed and improved.
S-92 Development Timeline
Public Introduction
First Ground Run
Flight Test Vehicle Completed
First Flight
Second Flight Test Vehicle Completed
Launch Customer Signed
Engine Receives FAA Certification
First Flight of a Customer-Configured Aircraft
First Flight of Production Configuration
First Flight of Military Configuration
FAA Type Certification Received
HIRF Testing Begins
Icing Tests Begin
JAR Part 29 Certification Received
First Delivery
Team S-92
- Japan’s Mitsubishi Heavy Industries (7.5% – main cabin)
- Spain’s Gamesa Aeronautica (7% – main rotor pylon, tailcone/transition section and composite interiors),
- Peoples Republic of China’s Jingdezhen Helicopter Group (2% – tail pylon and horizontal stabilizer)
- Taiwan’s Aero Industrial Development Corporation (AIDC) (6.5% – Cockpit Structure)
- Brazil’s Embraer (4% – sponsons complete with fuel system and landing gear).
- #1 aircraft, the ground test vehicle, was scheduled for 350 hours including 200 hours to certify the main gearbox.
- #2 aircraft, the first flight aircraft, was scheduled for 340 hours of flying
- #3 aircraft was closest to the production aircraft and focused on the aircraft’s operating systems. These systems included the auxiliary power unit, the engines Full Authority Digital Electronic Controls (FADEC), Automatic Flight Control System (AFCS) and engine development.
- #4 aircraft was the acoustics and options development platform and scheduled for 124 hours of flying.
- #5 aircraft, a utility configured aircraft was scheduled for 480 hours of flying at maximum gross weight and external load testing
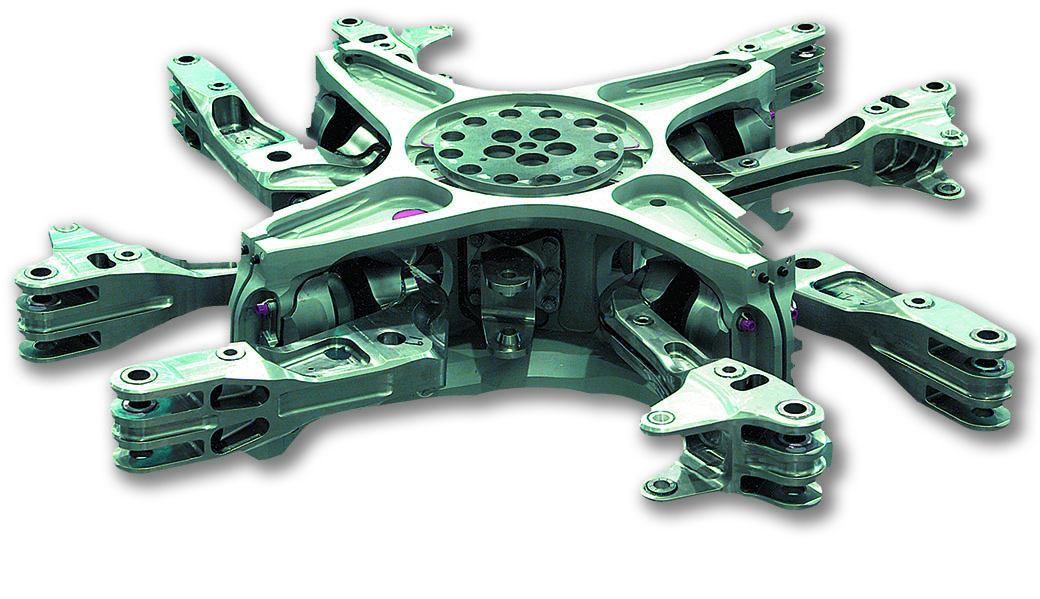
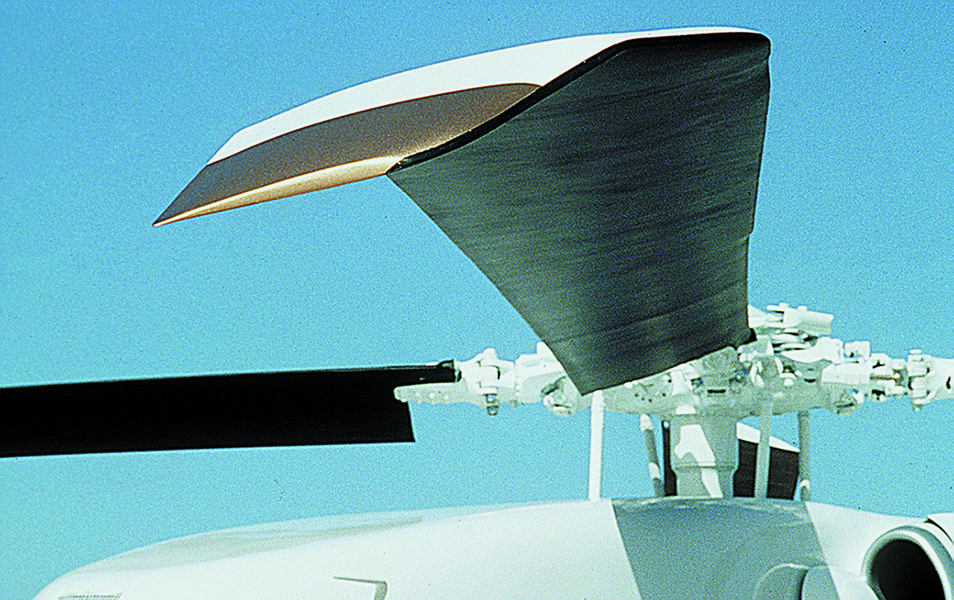
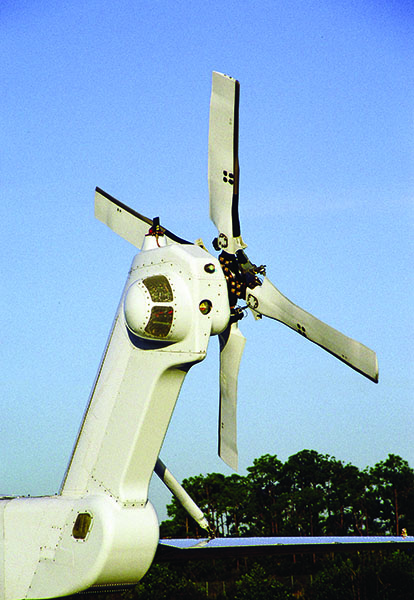
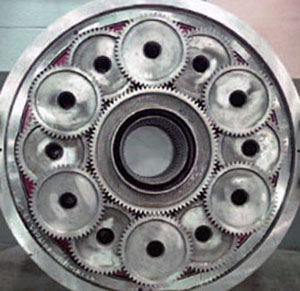
utilizes advanced materials for long life.
Configuration Features
Aircraft Component | Features |
---|---|
Airframe | |
Cockpit | |
Powerplant and Fuel System | |
Rotor and Drive System | |
Electrical |
Advanced Cockpit and Onboard Systems
General Arrangement Drawing
S-92 Optional Equipment
Aircraft Component | Optional Equipment |
---|---|
Airframe and Rotors | |
Furnishings | |
Propulsion / Fuel Systems | |
Electrical Systems and Lighting | |
Avionics | |
Special Mission Equipment |
General Characteristics and Performance
Performance Standard Day, Sea Level at 26,150 lb/11,861 kg gross weight | |
---|---|
Maximum speed (Vne) | 165 kts / 306 km/hr |
Maximum continuous cruise speed | 153 kts / 284 km/hr |
Long range cruise speed | 139 kts / 258 km/hr |
Range: offshore configuration (3,000 ft, ISA plus 10°C.) – with 19 passengers and 30-minutes reserve plus 10% | 444 nm / 823 km |
Range: offshore configuration (3,000 ft, ISA plus 10°C.) – with 19 passengers and no reserve | 544 nm / 1,008 km |
Maximum range with internal auxiliary fuel (370 gallons) | 726 nm / 1,345 km |
Service ceiling | 15,000 ft / 4,572 m |
Hover ceiling out-of-ground effect | 7,125 ft / 2,172 m |
Hover ceiling in-ground effect | 11,320 ft / 3,450 m |
Weights | |
---|---|
Maximum takeoff gross weight – internal load | 26,150 lb / 11,861 kg |
Maximum takeoff gross weight – external load | 28,300 lb / 12,837 kg |
Maximum external load | 10,000 lb / 4,536 kg |
Weight empty, offshore oil | 15,900 lb / 7,212 kg |
Weight empty, airline | 15,600 lb / 7,076 kg |
Weight empty, search and rescue | 16,200 lb / 7,348 kg |
Weight empty, 10-place executive transport | 17,200 lb / 7,801 kg |
Maximum fuel load, (internal, standard) | 5,130 lb / 2,327 kg |
General Data | |
---|---|
Crew seating capacity | 2 |
Seating capacity, airline-style seating | 19-24 passengers |
Seating capacity, utility side facing seating | 22 passengers |
Baggage compartment volume | 140 cu ft / 4.0 cu m |
Fuel capacity (internal, standard) | 760 US gal / 2,877 L |
Powerplant Ratings per engine, Standard Day at Sea Level | |
---|---|
Engine quantity and type | Two General Electric CT7-8A |
Twin engine takeoff, 5 minutes | 2,520 shp / 1,879 kw |
Twin engine, 30 minutes | 2,336 shp / 1,742 kw |
Maximum continuous | 2,043 shp / 1,524 kw |
OEI, 30 seconds | 2,600 shp / 1,912 kw |
OEI, 2 minutes | 2,520 shp / 1,879 kw |
OEI, 30 minutes | 2,498 shp / 1,863 kw |
Aircraft Dimensions | |
---|---|
Main rotor diameter (blade tip circle) | 56′ 4″ / 17.17 m |
Tail rotor diameter (blade tip circle) | 11′ 0″ / 3.35 m |
Fuselage length | 56′ 2″ / 17.10 m |
Fuselage width | 14′ 2″ / 4.32 m |
Length over-all (including rotors) | 68′ 6″ / 20.88 m |
Height over-all – to tip of tail rotor, positioned vertically | 17′ 11″ / 5.47 m |
Height over-all – to tip of tail rotor, positioned diagonally | 16′ 10″ / 5.12 m |
Width (including horizontal stabilizer) | 17′ 3″ / 5.26 m |
Width (blades parked at 45° to fuselage) | 40′ 0″ / 12.36 m |
Main landing gear tread | 10′ 5″ / 3.18 m |
Wheel base | 20′ 4″ / 6.20 m |
Passenger cabin length (with bulkhead) | 20′ 0″ / 6.10 m |
Passenger cabin width | 6′ 7″ / 2.01 m |
Passenger cabin height | 6′ 0″ / 1.83 m |
Production History
- by Vinny Devine
Related Articles
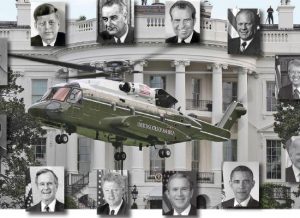
Sikorsky Serves the Presidents
Sikorsky Aircraft has engineered, built, and supported the Presidential helicopters since 1957.
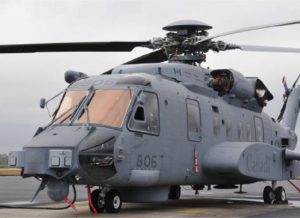
Sikorsky’s Sub Hunters
Today’s MH-60R gives the U.S. Navy the world’s most advanced ASW helicopter. However, the potential of the helicopter in ASW was recognized even before the Navy and Coast Guard flew their first Sikorsky R-4s in World War II.
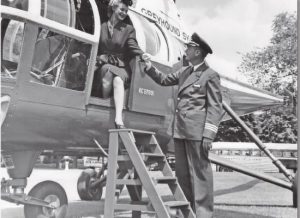
Sikorsky Helicopters in Airline Service
Early in the evolution of Sikorsky helicopters, Igor Sikorsky and his team envisioned scheduled passenger flights serving major cities.
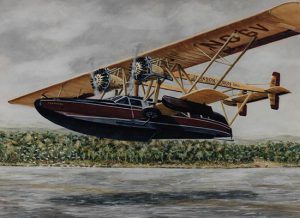
Sikorsky Aircraft Color Schemes
This issue of the newsletter illustrates some of the artistic variations in the exterior color schemes of aircraft delivered during Igor Sikorsky’s three careers.
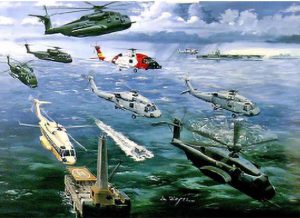
Sikorsky Aircraft Paintings by Andy Whyte
This issue of the newsletter is devoted to the aircraft designs and paintings by Andy Whyte, who had a 40 year career at Sikorsky Aircraft.
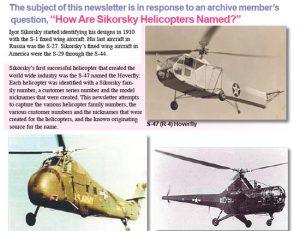
How Sikorsky Helicopters Are Named
The subject of this newsletter is in response to an archive member’s question, “How Are Sikorsky Helicopters Named?”
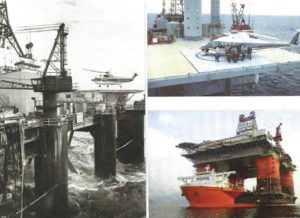
Revolutionizing Transportation in the 1950s
Igor Sikorsky’s large cabin single main rotor helicopters revolutionized the energy, health and other industry’s transportation requirements during the 1950s.
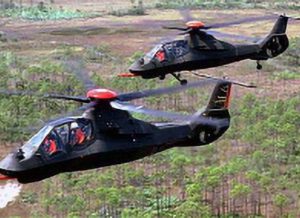
Sikorsky Aircraft in the 1990s
During the 1990s Sikorsky Aircraft produced the H-60 Hawks and the S-76 while developing the Boeing Sikorsky RAH-66 Comanche and the S-92 helicopters.
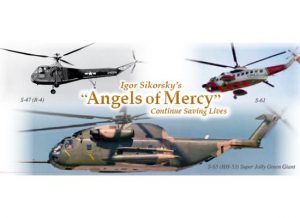
70th Anniv. of the First Helicopter Humanitarian Mission
Igor Sikorsky’s “Angels of Mercy” continue to save lives. 2014 marks the 70th anniversary of the first helicopter humanitarian mission in the world.
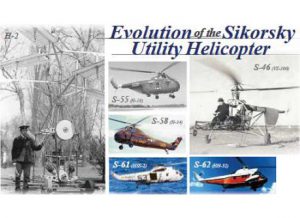
Evolution of the Sikorsky Utility Helicopter
This newsletter focuses on the evolution of Sikorsky utility helicopters.